What Kind of Maintenance and Repairs Do Commercial Vehicles Need?
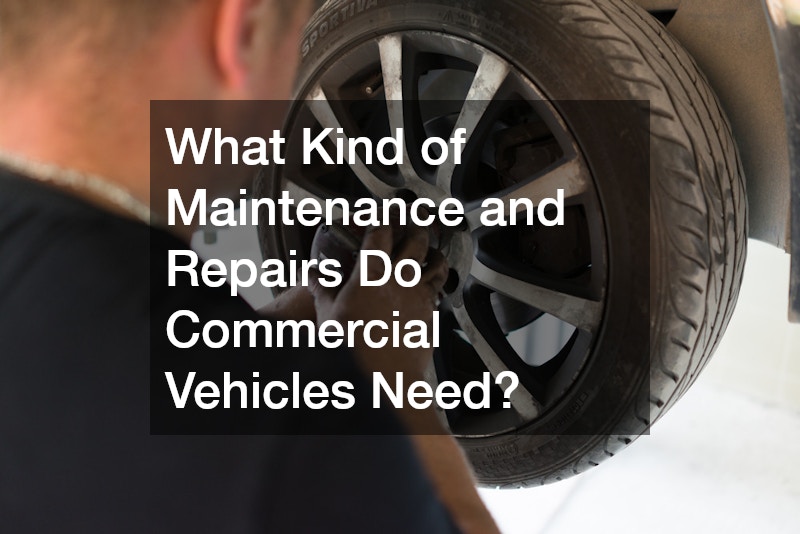
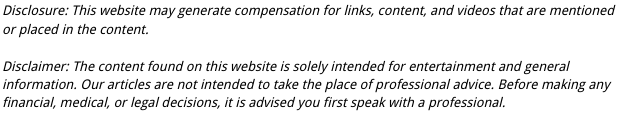
Commercial vehicles form the backbone of countless industries, handling everything from transporting goods across state lines to lifting and moving heavy loads on construction sites. Whether you operate a small fleet of vans or manage a variety of specialized equipment like crane trucks and fork trucks, maintaining these vehicles is crucial for safety, reliability, and cost-effectiveness. A well-serviced commercial vehicle not only reduces the risk of breakdowns but also prolongs its operational lifespan. In other words, regular checks, timely repairs, and thorough inspections aren’t just a box to tick—they’re essential components of a successful operation.
Ultimately, whether you run a single truck or manage a large fleet that includes tow trucks, mobile cranes, and specialized rigging equipment, the goal is the same: to keep the wheels turning safely and efficiently. Throughout this blog, we’ll outline key areas of focus and offer practical tips to help you stay on top of maintenance schedules. We’ll also identify some of the unique repair needs that arise for different types of commercial vehicles and heavy machinery. With this knowledge, you can make informed decisions that help ensure your fleet runs at peak performance year-round.
Why Maintenance Matters for Commercial Fleets
Running a commercial fleet—be it a handful of box trucks or a series of heavy-duty rigs—comes with a host of responsibilities. Chief among these is ensuring that every vehicle operates safely on public roads and work sites. In many cases, these vehicles are heavier, larger, and more complex than typical passenger cars. They may also handle dangerous or high-value loads. Failing to maintain them can lead to breakdowns that disrupt your schedule or, worse, accidents that cause serious injury or property damage.
Economics also play a significant role in the importance of maintenance. Unplanned downtime is expensive. When a truck carrying critical cargo breaks down, entire supply chains can be thrown off schedule, impacting not just the carrier but also clients awaiting their goods. Furthermore, small mechanical issues left unchecked often escalate into costly repairs. For example, ignoring a minor brake problem could eventually lead to damage to the rotors and other components, requiring a far more expensive overhaul.
Image and reputation are additional factors. If you run a towing service or offer rock hauling services, a well-kept vehicle sends a message of professionalism and reliability. A rusted, sputtering rig does little to inspire confidence in potential clients. The same goes for a fleet of vehicles used by a moving company—people want to trust their prized possessions to professionals who clearly take pride in their equipment.
Lastly, legal compliance cannot be overlooked. Many jurisdictions require commercial vehicles to pass regular inspections and meet stringent safety standards. Neglecting maintenance can lead to fines, legal complications, or the revocation of operating licenses. In the most extreme scenarios, serious mechanical failures can lead to accidents that result in lawsuits or criminal charges. Therefore, staying on top of maintenance is not just a matter of good business sense; it’s often a regulatory requirement.
Common Maintenance Tasks for Commercial Vehicles
-
Oil and Fluid Changes
Much like passenger cars, commercial vehicles need regular oil changes to keep engines running smoothly. The frequency of these changes may vary based on mileage, engine type, and operating conditions. Hydraulic fluids and transmission oils also demand periodic checks and replacements, particularly for vehicles like tow trucks that use hydraulic systems to lift and tow other automobiles. -
Tire Inspections and Rotations
For vehicles carrying heavy loads or traveling long distances, tires wear out more quickly. Routine checks for tread depth, proper inflation, and signs of uneven wear can prevent blowouts on the road. Regular rotation helps distribute wear evenly, extending tire life and improving fuel efficiency. -
Brake System Checks
Commercial vehicles often bear substantial weights, making fully functional brakes a top priority. Brake pads, rotors, and fluids should be evaluated routinely. Any squealing, pulsing, or reduced responsiveness is an immediate red flag. In the case of heavy rigs and trailers, air brake systems require specialized knowledge for maintenance. -
Electrical System Assessments
Modern commercial vehicles come equipped with complex electrical systems that control everything from engine performance to safety features. Batteries, alternators, and wiring should be inspected to avoid issues like power failure, dim lighting, or malfunctioning safety sensors. -
Cooling System Maintenance
Commercial engines generate significant heat, particularly under heavy loads. Properly functioning radiators, hoses, and coolant levels are critical to preventing overheating. Routine flushes and inspections for leaks can sidestep major engine damage. -
Inspection of Suspension and Steering
Heavy loads can put a serious strain on suspension components like shocks, struts, and bearings. Poor suspension not only makes for an uncomfortable ride but can also pose safety risks by impairing vehicle handling. -
Filter Replacements
Air, fuel, and oil filters all contribute to engine health. Clogged filters can affect performance, fuel efficiency, and emissions. Regular replacement keeps engine systems clean and efficient. -
General Safety Features
Elements like lights, mirrors, windshield wipers, and seat belts might seem minor, but they’re crucial for day-to-day safety. Regularly verifying that these are working correctly can prevent accidents and avoid legal infractions.
Incorporating these tasks into a well-structured preventative maintenance schedule helps keep commercial vehicles in top form. Doing so can also help you detect early signs of more significant problems. While it’s true that all vehicles undergo wear and tear, catching issues before they escalate can save both time and money. This is especially true in fast-paced industries like moving companies or those that rely on complex machinery such as fork trucks for warehouse operations.
Specialized Vehicle Requirements
Not all commercial vehicles are created equal. While a general cargo van might stick to a standard routine of oil changes and tire rotations, specialized equipment demands additional care. Understanding these unique requirements is key to preventing breakdowns and prolonging the life of each vehicle in your fleet.
Forklifts and Fork Trucks
Forklifts and similar fork trucks are indispensable in warehouses and loading bays. Yet they operate in environments where they frequently lift heavy loads and make tight maneuvers. This repetitive strain heightens the risk of hydraulic system leaks, worn-out forks, or transmission troubles. Regular forklift repair checks may involve assessing the hydraulic lift cylinders, ensuring forks remain straight and free of cracks, and verifying the proper function of the mast assembly. Additionally, battery-powered models require careful battery maintenance to prevent power shortages.
Tow Trucks
Tow trucks typically endure harsh conditions—long hours on the road, variable weather, and repeated lifting tasks. They rely heavily on hydraulic or winch systems to haul vehicles, meaning these components should undergo routine checks. From ensuring the cables and pulleys function smoothly to verifying the operation of warning lights and signals, tow truck maintenance can be intricate. Neglecting any detail can result in an inability to safely secure a towed vehicle or cause mechanical failure mid-transit.
Vehicles Used by Dumpster Rentals
Trucks utilized for dumpster rentals face unique strains, such as lifting and hauling large receptacles of trash or construction debris. The mechanical arms and hoist systems that raise dumpsters on and off the truck bed need regular lubrication and inspection. Rust, metal fatigue, or hydraulic leaks can lead to catastrophic failures. Coupled with the weight of full dumpsters, tires, brakes, and suspension all face increased stress, warranting frequent scrutiny.
Rock Hauling Services
Vehicles transporting heavy aggregates like gravel or stones often operate in rough terrains or construction sites. Extra stress on suspensions, axles, and tires is par for the course. Regular cleaning to remove debris and dirt buildup around moving parts is equally crucial. Dirty hydraulic pistons or wheel wells can accelerate wear and even jam important mechanisms.
Crane Rental Trucks
For companies offering crane rental, the stakes are high. Cranes involve complex hydraulic, pneumatic, and mechanical systems, each with zero tolerance for flaws. Crane booms, cables, and rigging components like hooks and shackles must pass frequent inspections to ensure they can manage the expected loads safely. Even minor cable frays or unusual gear noises can foreshadow an impending failure, which could pose serious safety hazards on a job site.
Tractors for Mobile Repairs
Agricultural or industrial tractors sometimes operate in remote or rural areas, making mobile tractor repairs a valuable service. These tractors endure dusty, muddy environments that challenge the performance of engines, transmissions, and cooling systems. Ensuring easy access to filters, fluids, and spare parts is vital for on-the-spot repairs. Mechanical breakdowns often happen far from repair shops, so a well-maintained tractor can mean the difference between completing a job and incurring expensive downtime.
By recognizing these specialized maintenance needs, businesses can create targeted service schedules. Being proactive reduces the risk of sudden failures, which can cause unsafe working conditions and expensive halts in productivity. For instance, a crane breakdown in the middle of a high-rise construction project can throw entire timelines off course, leading to penalty fees or lost revenue. Similarly, ignoring routine fork truck maintenance could hamper warehouse efficiency, delaying shipments and damaging client relationships.
Addressing Repairs in a Timely Manner
Even with meticulous preventative care, commercial vehicles can and do experience mechanical failures. The key is to address these issues promptly and effectively. Allowing small problems to linger often transforms them into major, expensive repairs. Rapid response to warning signs like unusual noises, dashboard alerts, and performance dips is essential. That means training drivers and operators to recognize red flags—an alerted driver can save a fleet manager thousands of dollars by catching a potential problem early.
When a problem does occur, deciding whether to fix it in-house or outsource it to a specialized repair service becomes the next step. If you have an experienced maintenance team and the necessary tools, doing certain repairs internally can save time and money. However, complex tasks—like a complete engine overhaul or forklift repair that involves the hydraulic mast—may require specialized skills and equipment best found at accredited service centers.
Having a network of reliable service providers is invaluable. Rigging companies or local hydraulic specialists can swiftly address issues unique to crane trucks, tow trucks, and other heavy equipment. Mobile tractor repairs, for instance, are particularly important for businesses operating in locations far from well-equipped garages. These on-site repair services can drastically cut downtime, eliminating the need to transport heavy machinery to distant shops.
The downtime associated with repairs is costly in multiple ways—lost productivity, delayed projects, and potentially tarnished business reputations. Minimizing that downtime hinges on excellent communication between drivers, mechanics, and fleet managers. Implementing a streamlined reporting system ensures that faults are documented immediately. Digital tracking tools also allow teams to keep precise records of every repair, from basic tire rotations to complex engine rebuilds. This data not only helps in scheduling future maintenance but also provides insights into recurring issues that may point to deeper structural or operational problems.
Coordinating Fleet Management Across Multiple Vehicle Types
For businesses that manage diverse fleets—ranging from standard cargo trucks to specialized vehicles like fork trucks or crane rigs—coordinating maintenance is a complex chore. Each vehicle type operates on different service intervals and may require distinct replacement parts, fluids, and inspections. This complexity can become overwhelming without a solid organizational strategy.
One effective approach is to implement fleet management software that centralizes maintenance schedules, parts inventory, and repair records. Digital solutions can send automated alerts when a service is due, and they can track specific parts like forklift forks, tow cables, or crane hooks. This level of organization reduces the chance of missing a critical service date. Some advanced platforms even integrate with telematics systems in the vehicles themselves, providing real-time data on engine performance, fuel efficiency, and other metrics.
Another essential component is assigning responsibilities clearly within your organization. If you have a designated fleet manager, they should maintain open lines of communication with drivers, warehouse managers, and any third-party service providers. For instance, if a trucking company also uses dumpster rentals, its fleet manager might liaise with different vendors for specialized parts or disposal protocols. Meanwhile, rigging companies contracted for crane operations may require detailed equipment logs to ensure everything meets regulatory requirements.
Operating across different industries—like moving companies that also handle specialized freight—often means adhering to various regulatory frameworks. Staying compliant may involve additional inspections or certifications. Planning ahead for these requirements and setting aside budgets for unexpected updates is part of successful multi-vehicle fleet management. By standardizing documentation and record-keeping processes, you’ll have an easier time proving compliance during audits or when renewing operational licenses.
Choosing the Right Repair Partners
Finding trusted repair shops or service partners is vital for any commercial fleet. However, selecting the right provider isn’t always straightforward. A local garage might handle routine oil changes or brake repairs adequately, but they may lack the capability to work on complex hydraulics for your crane rental unit. Similarly, a standard auto shop may not be equipped to manage specialized tasks like forklift repair.
Start by researching businesses that specialize in the type of commercial vehicle you need serviced. Ask about the shop’s experience with similar fleets and any certifications or training programs their mechanics have completed. For example, if you operate a fleet of tow trucks, you’ll want a repair service familiar with hydraulics, winches, and even the specialized lighting systems these vehicles require. Reviews and word-of-mouth recommendations can also guide you toward dependable providers.
Another consideration is the geographical coverage of your business. If your operations span multiple states, having a single repair shop in one location may not be practical. In such cases, establishing relationships with mobile tractor repairs or traveling mechanic services could be beneficial. These services come to you, significantly cutting down on the need to transport broken vehicles over long distances. For businesses like rock hauling services that may need on-the-spot fixes in remote areas, mobile solutions can be game-changers.
Price, of course, is always a factor. But going with the cheapest option often proves shortsighted. A single shoddy repair can lead to bigger issues later, costing more in extended downtime or subsequent fixes. Focus on quality and reliability first, then negotiate the best deal possible. Sometimes, service contracts or bulk maintenance agreements can lower individual repair costs. If you run multiple vehicles through the same shop, you may qualify for discounted rates, expedited service, or extended warranties on parts and labor.
Strategies for Minimizing Downtime
Downtime is the enemy of productivity, especially in sectors like moving companies where customers often book services weeks or months in advance. Having a truck out of commission can create scheduling chaos, forcing you to reschedule deliveries or turn away business. Therefore, finding ways to reduce downtime is crucial. This often begins with preventative maintenance. By regularly servicing your vehicles, you minimize the risk of unexpected failures.
Another strategy is to maintain a small backup fleet or have contracts in place for rentals. For instance, if one of your primary trucks goes into the shop, you can quickly rent a replacement, ensuring your operations continue. Some businesses partner with local general contractors or equipment providers that offer crane rental or other machinery on short notice. This arrangement can be mutually beneficial—your partner gains business, and you gain peace of mind knowing a replacement vehicle is a phone call away.
Preemptive parts stocking can also reduce downtime. Keeping commonly needed components—like filters, belts, or brake pads—in your own inventory allows for quick fixes. This approach is especially effective for fleets where certain repairs, such as changing a worn belt, can be handled by in-house mechanics or adequately trained drivers. In such scenarios, having the right parts on hand can get a vehicle back in service within hours instead of days.
Scheduling and logistics also matter. Plan your maintenance during off-peak hours or slower business seasons. If you know that weekends are less busy for your towing service, allocate some vehicles for thorough inspections and minor repairs during that period. This approach spreads out downtime, preventing a situation where multiple vehicles are off the road simultaneously. In the event that you must take several vehicles offline at once—perhaps due to a widespread recall or major mechanical issue—good planning and open communication with clients can help mitigate the impact on your company’s reputation.
Record-Keeping and Regulatory Compliance
Maintaining comprehensive records is far more than a bureaucratic chore—it’s a roadmap of your fleet’s health history. Detailed logs should include maintenance schedules, repairs completed, parts replaced, and even oil change intervals. These records are invaluable for diagnosing recurring problems, predicting when certain parts will wear out, and budgeting for upcoming maintenance cycles. Moreover, they are often a legal necessity. Commercial vehicles are frequently subject to inspections by government agencies, especially those carrying heavy or potentially dangerous loads.
Businesses offering crane rental or employing rigging companies might face rigorous audits to ensure public safety on large-scale construction sites. Similarly, a trucking company that transports hazardous materials must adhere to stringent federal and state regulations. Falsifying or neglecting maintenance records can lead to heavy penalties, insurance complications, and, in extreme cases, forced closure. Organized record-keeping is your best defense, proving that you’ve consistently met or exceeded safety standards.
In today’s digital age, software solutions can automate much of this process. Fleet management platforms can log every service appointment, track mileage, and send reminders for upcoming tasks. Integration with telematics systems adds another layer of detail, providing real-time data on driving habits, fuel consumption, and performance metrics. Such systems can be particularly helpful for large fleets that include a range of vehicles, from forklifts to tractor-trailers. Operators receive alerts when forklift repair is due, or when it’s time for a mobile tractor service call. Automated reporting also eases the burden of producing documentation during compliance checks.
Lastly, it’s wise to designate a person—or team—responsible for keeping these records current. Whether it’s an internal fleet manager or an external service provider, accountability ensures that no detail slips through the cracks. During audits or legal inquiries, up-to-date records can stand as a testament to your commitment to safety and operational excellence.
Maintenance and repair for commercial vehicles is not just a matter of mechanical upkeep—it’s a core element of any thriving, reputable business. From hydraulic inspections for fork trucks to specialized engine work through mobile tractor repairs, every aspect of servicing these vehicles contributes to an operation’s smooth and efficient functioning. A broken-down truck can disrupt entire supply chains, derail construction schedules, or leave customers without the services they need. Therefore, timely and thorough maintenance plays a pivotal role in meeting client expectations, staying compliant with regulations, and safeguarding your investment.