Understanding Industrial Air Compressors Types, Working Principles, and Applications
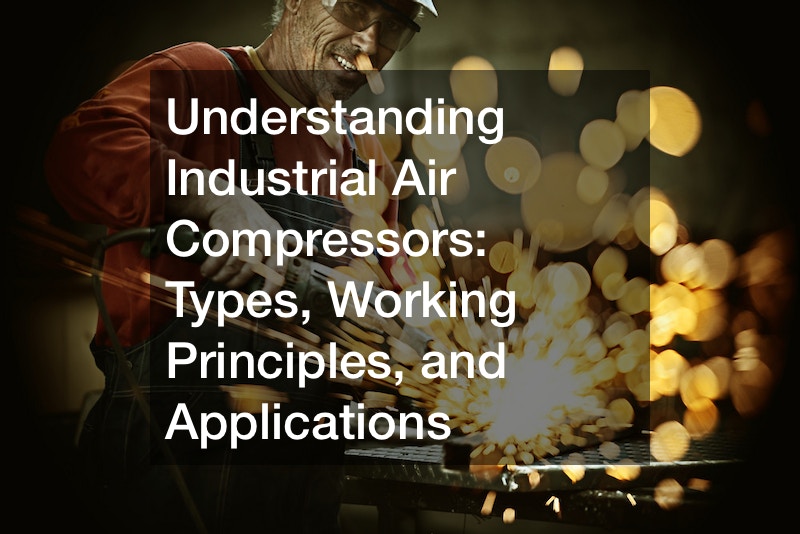
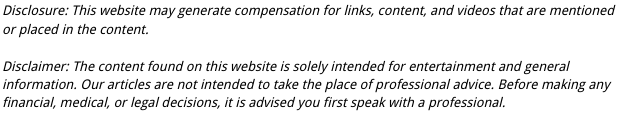
In the dynamic world of automotive technology, the role of industrial air compressors is paramount. These mechanical workhorses, essential in various automotive applications, come in diverse types, each with unique working principles and specialized applications.
Reciprocating compressors, commonly used in workshops, utilize pistons to compress air. However, issues arise from heat generated during compression, limiting their output pressure.
Conversely, multistage compressors offer higher pressures by employing multiple stages of compression and cooling.
Diaphragm compressors, integral in industries like food processing, maintain air purity by preventing contact between compressed air and lubricated parts. Yet, their effectiveness can be limited due to membrane constraints.
The innovative rotary compressor, with its pulsation-free airflow, offers versatility and quiet operation. These compressors find applications beyond automotive, such as in wastewater treatment, fish breeding, and dust collection, proving their adaptability and efficiency.
Understanding these compressor types empowers automotive professionals to make informed choices for specific tasks. Whether it’s powering pneumatic tools, managing air supply in engine testing, or aiding in assembly line operations, the right industrial air compressor plays a pivotal role.
In the realm of automotive technology, comprehending industrial air compressors – their nuances, strengths, and applications – is indispensable. These machines serve as the backbone, enhancing efficiency and productivity across various automotive operations.
.